BIM Connections
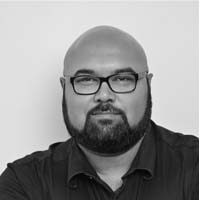
How BIM technology can help the collaborative process from conception to completion of a project

Over the last few years, there has been a significant change in the way Building Information Modelling (BIM) is viewed in the construction industry in the GCC region. While the technology was initially treated with some suspicion by consultants and contractors in the Middle East, a succession of positive project outcomes has helped convince the construction industry that BIM should be the way forward in the future.
These optimistic vibes have been further reinforced by the support of governments across the region for BIM. Countries like Jordan, Qatar and Saudi Arabia have all espoused support for projects that use the software, after having seen the benefits that come from implementing it on their construction projects. However, while it is undeniably heartening to see the adoption of BIM technology in the region, given the long struggle fought by its advocates, the next stage in the natural evolutionary process must start to take place, experts have told Big Project ME.
This means that the case for BIM to be used across all facets of the construction process must be considered, says Dr Ozan Koseoglu, BIM leader at TAV Construction.
“Even if you have a complete BIM model that was generated at the design phase, you still have lots of challenges on site,” he says. “The key issue is to bring people together. Forget the technology, it’s about the people and the processes. These are the key things which I think are very important to look at.”
“These two things are not easy to change. It really needs a different approach to change the people and the processes. You can draw the process maps and the flowcharts, but at the end of the day, the magic of BIM lies in how you bring people together within a virtual collaborative working environment,” Koseoglu adds.
One way that this could be done is by having the governments take a leading role in encouraging BIM to be used, not just at the design and planning stage, but also throughout the construction process and even afterwards, during the maintenance phase.
Phil Auguste, head of Business Development for Causeway, cites Singapore as an example of how this can work.
“Singapore is quite advanced and through the Building Contractors Association (BCA), have made funding available for any one that’s working in the public sector (construction). 50% of their expenditure on BIM software could be reclaimed under a government grant, so they’re putting a lot of weight behind it,” he explains.
“Now the UK is following suit, what they’re saying is that anyone working on government projects by 2016, needs to be combined with level II BIM.”
“In very simple terms, it’s the ability to unlock the key data caught in disparate systems, for whatever process you’re managing. That could be a consultant producing a cost plan, or a contractor producing a detailed estimate,” he adds.
Internationally, this is a growing trend in the construction industry, where professionals have realised that BIM can push integration and improve design outcomes. Tracy Douglas, a senior industry marketing manager at Autodesk, tells Big Project ME that a lesson could be learned from the manufacturing industry, which has long used concurrent engineering practices, coupled with digital product prototypes, to control product outcomes.
“At companies like Boeing and Toyota, product teams comprised of the various disciplines collaborate – from the outset – on all facets of a product’s lifecycle to ensure that the emerging product design includes the desired characteristics that are needed to bring a product to market,” she explains.
“Their product development processes rely upon information-rich digital models that are used for product design, as well as manufacturing, field support and so on.”
Therefore, integrated project delivery, enabled by BIM, can be based on a similar strategy, Douglas says. With cross-functional project teams collaborating on a building’s design, construction and lifecycle management for optimised owned outcomes is possible, using collaborative, model-based technology as a platform.
Koseoglu adds that contractors should be running a BIM model before they even go onsite, thereby allowing themselves to be best prepared for any issues that may crop up, which they always will.
“What (benefits) will it bring a contractor? It will definitely reduce the cost because you oversee the issues before going onsite. Once you go onsite, you face a lot of issues, particularly in design, while the biggest issues tend to be client requests, design issues and build up issues. So by using BIM forecasts, you can oversee all of these issues before even going onsite,” he explains.
“In terms of cost-wise issues, the major reason why projects are not successful are because of cost and time overruns. These are the key things: cost, time and quality. Once you lose cost and time, then you’re going to be compromised for quality as well, as many projects are,” he points out.
“If you have proper BIM implementation, building it digitally, and applying it to the lifecycle, then you can control the cost overruns and at least you can see where they (cost overruns) are going to be, before even building,” he adds.
Tracy Douglas adds that contractors and consultants can contribute construction knowledge to existing design models by having the same model generate the information necessary to provide to all project participants.
“This concept is the premise behind the AIA Integrated Project Delivery system, with all participants actively involved from the very beginning to the very end and evolving/sharing the same model along the way,” she says.
“The model itself can be depicted to any level of detail imaginable and is, therefore, the single source for the design document and the shop drawing level of detail. This detail completely eliminates the cost and time associated with an iterative shop drawing process and, yet, it improves the accuracy of the translation.”
Phil Auguste points out that accuracy when designing and planning is a fundamental requirement for anyone on a project. As such, he advocates that BIM be used to ensure that all facets of estimation and planning are spot on.
“I think by unlocking the data within BIM – and making the systems used interoperable, you can get more accuracy on price, timeline; in-fact you can use BIM to drive pretty much everything. From the source data within the model, you can then effectively manage the whole process, from start to finish. From feasibility, from the first time you think of a project, through design, cost planning, estimation, build to handover, to lifecycle management, retaining and using that data from start to finish,” he asserts.
Furthermore, while it’s understandable that BIM can be used for the design, planning and construction stage of the project, what’s often ignored, or simply not known, is how the software and technology can have a positive impact on the lifecycle of the building.
Jacqueline Walpole, business analyst for FSI FM, a UK-based FM firm, tells Big Project ME that there’s a very obvious impact during the design and construction phrase, but that if people consider the ‘RIBA Plan of Work’, the final phase of any project are the occupation and operation.
“BIM can allow predictability of the maintenance, equipment lifecycle, sustainability and energy costs, and therefore the ability to make appropriate design and installation decisions about the whole life cost,” she explains.
Walpole says that there are benefits of having a building up and running with all FM systems in place prior to handover.
“The whole concept of a ‘soft landing’ is relatively new and is being fully supported by companies such as FSI with the integration of our Concept Evolution IWMS/CAFM software to BIM databases,” she says. “We can provide consultancy on ensuring that FM is considered at an early stage and help in developing your BIM protocol and BIM EIR (Employer Information Requirements) to make sure a clear specification of what data is stored and how it is attached in the BIM is of use for the operational phase of the building.
“During the operation, if the BIM, it can provide an electronic O&M manual for all to view and make re-tendering of maintenance contracts, space management and refurbishment far simpler.”
The onus is now on the construction industry in the region to seek out ways to challenge and adapt the technology to best suit their own needs. It’s certainly proved to be up to the task.