Himoinsa provides quick back-up power for Doha Festival City
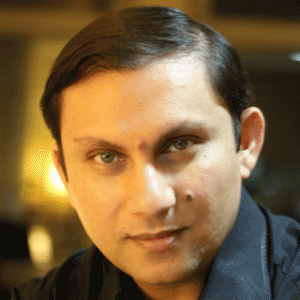
When the Qatar mall wanted emergency stand-by power, it turned to the Spanish generator giant Himoinsa to install an 8.7MVA back-up system that comes on in just seven seconds

Imagine you’re spending your Friday in one of the mega malls that dot the main cities of the GCC region – and the power goes out. In an instant all the brightness, the multi-coloured lights, the eye-catching displays, the glitz and glamour is replaced by the near-darkness that a completely enclosed structure such as a mall will be in when unlit. Unimaginable. But plausible.
For at least one mega mall in the region, however, that unimaginable scenario, if it ever happened, would last all of only seven seconds. Thanks to generator giant Himoinsa and its distributor FAMCO, Qatar’s spanking new Doha Festival City (DFC) mall has ensured the continuity of its power supply by installing generator sets that start up in record time in the event of a failure in the electricity grid.
The 670,000sqm leisure destination will be home to more than 500 stores and restaurants, and a world-class entertainment complex, with both indoor and outdoor attractions unique to Qatar. With footfall expected to exceed 1.6 million people per month, safety and the proper operation of all business units at the mall will rely heavily on a system capable of supplying power in the event of an emergency. Not only that, such a system must meet the stringent requirements that the Qatar Civil Defence has envisaged for public spaces.
Enter Himoinsa and its HTW-1745 T5 generator sets. To feed such a huge complex and to respond quickly in the event of a power cut, the Murcia-based company came up with the solution of using five of the sets, each of which produce 1.736kVA of stand-by energy, making for a total of 8.7MVA of stand-by power. The units feature Mitsubishi engines and Stamford alternators that have been oversized and fitted with sophisticated control systems that synchronise the gensets. The machines respond seven seconds after any power failure and are also prepared to work in a maximum ambient temperature of 55 degrees Celsius. But more about that later.
To begin at the beginning, a lot of preparatory work and careful planning went into the project, both from the project owners and contractors as well as from Himoinsa. Speaking to CMME about the entire process, Massimo Broto, sales engineering manager at Himoinsa, says: “We actually got in touch with the contractor through our Middle East branch in Dubai, and our regional distributor FAMCO, more than a year before we delivered the units. We found out all the details of the project, especially its power requirements, and held detailed discussions about those requirements with the project engineers, giving them our advice and recommendations.”
In typical Himoinsa tradition of being fully involved with their projects, those recommendations were in great detail, such as a consultant would give. Brotto adds: “We advised them about how to prepare the building for generator installation, how to manage the access and how to adapt the electric connections for the genset incorporation.
“The most discussed topic was about the building management system because there were some very tough specifications to follow on the project, which included many procedures on the management of the circuit breakers for the generator as well as the mains, which we do not commonly see. For us it was a challenge because there were a lot of safety procedures, simulations and synchronising. They asked for something which is more complex than the common practice.”
Thanks to a detailed programming study of the control units, and after having subjected the units to multiple highly demanding tests, Himoinsa was able to guarantee a synchronised start-up time that, in fact, exceeded the project’s technical specifications.
The objective was to guarantee an uninterrupted supply of electricity with generator sets capable of starting up in synchronicity with 100% of the load and in less than 10 seconds in the event of a failure in the supply of electric power.
Speaking about the challenging requirements, Terry McGuire, regional general manager, FAMCO, says: “The biggest challenge of this project was to meet the stringent requirements of Qatar Civil Defence. We needed to prove that all the gensets would be able to run from a dead start, synchronise and produce power within 10 seconds. We managed to show this by the factory witness test, where we achieved 7.8 seconds, and we also proved the same results on site.”
Himoinsa’s technical team subjected the five generator sets to a stringent test protocol to predict and guarantee a suitable response, pushing the units to the limit of their operational capacity. Brotto adds: “We measured both the synchronisation times and the quality of the voltage and the current. We ran single-step load impact tests at 100%, guaranteeing a stable and rapid recuperation. We also simulated all the possible combinations of breakdowns to ensure that the system would respond in the event of a failure. And we did not endorse the tests until we had established that the units were reliable in all these situations.”
Of course having a tried, tested and proven product in the HTW-1745 T5 generator helped matters, “but we pushed it as a model to an extreme performance level”, Brotto adds.
“The PI734E alternator was oversized to 1900kVA and fitted with a programmable Digital Voltage Governor capable of providing an extremely quick response. Also, at the mechanical level, we guaranteed the temperature controls in the bearings and the winding so that they can operate safely and continuously, even for longer periods of time, were that to prove necessary.”
The gensets were fitted with Woodward speed controls to guarantee quick and reliable response. The Japanese technology Mitsubishi S16R PTA engines had all their vital parameters such as the oil pressure, the temperature of the water, the oil and the exhaust fumes measured continuously, making them communicate with a monitoring system controlling the condition of the engine. To ensure a fast response in the event of a grid failure, a water pre-heating system was added, as was a battery charger that ensures maximum efficiency.
Himoinsa used Deep Sea control units that allow for syncing directly with a Dead Bus, thereby saving time manoeuvring the motorised circuit breakers in each set. The control systems are also connected to a PLC that handles the running of the generator sets and their interactions with the mall’s distribution system.
With Himoinsa’s long track record of delivering units to the region, the company is adept at dealing with the harsh demands of the region’s climate – and the DFC generators were no exceptions. Brotto explains: “We are well acquainted with the demands that the GCC’s conditions place on any machine, so we have some standardised practices in place for the region’s heat and humidity. The first is to size the cooling package properly, which we always do when we supply a machine to this region. Another aspect that has been taken care of in this project is to oversize the engine and the alternator… in other words we have adapted the complete set specifically for the unique demands of this project.”
But now that the project has gone live, the generators will only be as good as the service and support they receive. And this is where Himoinsa’s dealer FAMCO comes in.
“An important part of our business is our local presence, which is taken care of by FAMCO. They will provide after sales service, routine maintenance and spare parts. Only in special cases when the issue is out of their control, will we provide support, first from our branch in Dubai and then from our headquarters in Murcia, if required,” explains Brotto, who adds that to maintain Himoinsa’s high quality levels, there are constant training programmes for both in-house personnel as well as those from partners all over the world.
“Our direct people, such as branch personnel, as well as technicians from dealers and partners, are all trained by our specialists and are ready to deliver our world class support locally to proper Himoinsa standards. For the DFC machines, that support will come from FAMCO. We are in this project together.”
Echoing his sentiments about the effort being a joint one, McGuire says: “To execute a complex project like this, we needed the full support of the Himoinsa engineering team, as the requirements were enormous and highly technical.”
That they have been successful is for all visitors to DFC to see. In the event of a power emergency, it’s a success that will be visible in seven seconds.
TECH SPECS
Location: Doha (Qatar)
Installed power: 5X1736 kVA = 8.7MVA stand-by power
Generator sets: 5 HTW-1745 T5 units
Dimensions: 5,238 x 2,043 x 2,600 mm (L x W x H)
Special configuration: Redundant emergency power supply with a seven-second start-up synchronised to a Dead Bus. Assumes 100% of the load in one single step. Redundant control panels.
Casablanca project: A beautiful friendship
Himoinsa is no stranger to large-scale back-up power projects in the wider Middle East and North Africa region. In fact, the company recently added another feather to its cap in Morocco, where two Himoinsa HDW-750 T5 generator sets are guaranteeing the supply of electricity to the 26-storey Casablanca Finance Centre (CFC), the first building in the city’s new financial district.
The tower will house the offices and headquarters of banks and financial institutions for whom any manner of power cut could entail losses of millions. Himoinsa says that to prevent this from happening in the event of a network failure, both generator sets will start working in parallel and will be able to supply up to 1.3MW of stand-by power.
Himoinsa’s engineering team has redesigned the generators’ standard canopy in order to adapt it to the rather small room in which they are housed. As the height of the room precluded a high-level air outlet, the exhaust system was changed ad hoc to expel the gases and the hot air from the radiator from the front.
Redouane Mouzani, the project’s head of engineering, the Spanish manufacturer was “the only company able to come up with a technical engineering solution adapted to the limitations of the room in the installation”.
“We chose Himoinsa because of their flexibility in designing and manufacturing of the gensets, and because their engineering team works so quickly.” Mouzani added.
Karim Housni Alaoui, project head for CEGELEC, the company in charge of the CFC tower project, adds: “We chose Himoinsa because they guaranteed an excellent after-sales service, a high availability of replacement parts, a quality product and because of how they quickly resolved the engineering challenges that the project presented.”